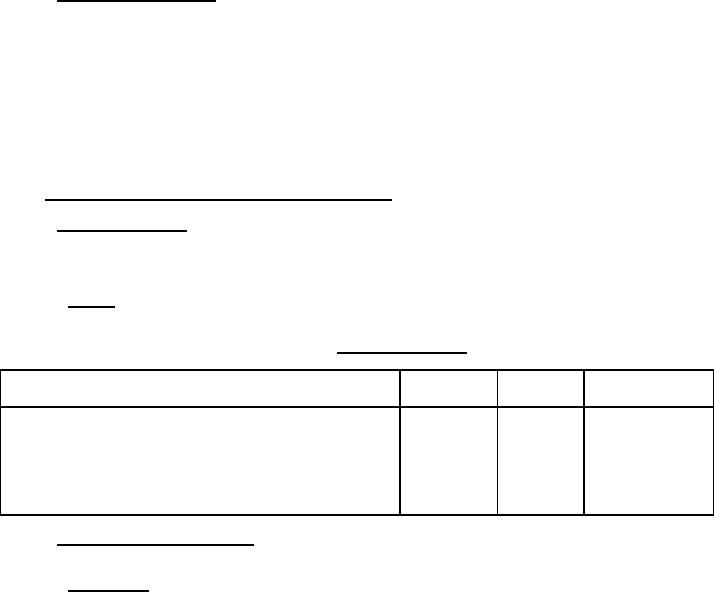
MIL-PRF-123D
4.4.4 Verification of qualification. Every 12 months, the manufacturer shall provide verification of qualification to
the qualifying activity. Continuation of qualification shall be based on meeting the following requirements:
a. MIL-STD-790 program.
b. Product design has not been modified.
c. Certification that the manufacturer still maintains the capabilities and facilities necessary to produce these
items.
d. Verification of the results of group A, group B, and group C inspections including identification of failed lots
and subgroups and failure modes.
4.5 In-process inspection and quality conformance inspection.
4.5.1 In-process inspection. Each production lot of parts shall be inspected in accordance with table X. The
nondestructive internal examination used (if other than ultrasonic examination) shall be approved by the qualifying
activity. Other screening examinations may be applied at the option of the manufacturer, as approved by the
qualifying activity.
4.5.1.1 Rework. Rework is not allowed on any operations including and subsequent to the formation of the slurry,
except for marking and lead rework.
TABLE X. In-process inspection.
Inspection
Requirement
Test method
Sample size
paragraph
paragraph
Nondestructive internal examination
100 percent
Pre-termination destructive physical analysis
Visual examination
100 percent
Pre-encapsulation terminal strength (leaded capacitors only)
Table XV
Post termination, unencapsulated destructive physical analysis
Table XVII, group I
4.5.2 Inspection of product for delivery. Inspection of product for delivery shall consist of groups A and B
inspection.
4.5.2.1 Inspection lot. An inspection/production lot shall consist of all capacitors of a single nominal
capacitance/voltage rating of one design, from the same dielectric material batch, and processed as a single lot
through all manufacturing steps on the same equipment. The lot may contain all available capacitance tolerances
for the nominal capacitance value. In addition, the lot shall conform to the following:
a. Raw materials, such as end terminations, solder, ceramic raw material, binders, and electrode ink, shall be
traceable to the same lot or batch and be from the same contractor.
b. A lot number shall be assigned before electrode printing (inking) and be manufactured from the same slurry
and cast on the same belt or comparable equipment (see 3.4).
c. A single mix of a basic ceramic formulation fired through one kiln with one temperature profile during the
process, with constant dielectric design, with, in general, no more than 20 percent variation in the number of
active dielectrics being assembled in one continuous buildup. Sublots may be allowed to provide a spread in
capacitance value to improve the yield. This will normally be done in the case of tight tolerances and low
capacitance. In some cases, more than 20 percent variation in the number of active dielectrics may be
required in these circumstances (see 3.3).
16
For Parts Inquires submit RFQ to Parts Hangar, Inc.
© Copyright 2015 Integrated Publishing, Inc.
A Service Disabled Veteran Owned Small Business