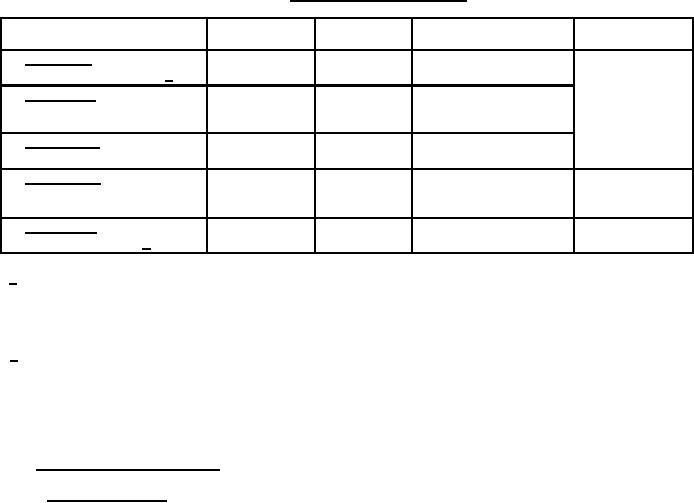
MIL-PRF-55365H
TABLE X. Group C inspection (ER only).
Inspection
Requirement
Method
Number of sample units
Number of failures
paragraph
paragraph
to be inspected
allowed
Subgroup I
Thermal shock (mounted) 1/
12
Subgroup II
Resistance to soldering heat
18
1
Moisture resistance
Subgroup III
Life (2,000 hours at +125°C)
24
Subgroup IV
Life (10,000 hours at +85°C)
25 minimum per style
See 4.4.4.1
FR (exponential only)
Subgroup V
Resistance to solvents 2/
8
0
1/ If the manufacturer can demonstrate that this test has been performed five consecutive times with zero failures,
this test, with the approval of the qualifying activity, can be performed on an annual basis. If the design,
material, construction or processing of the part is changed or, if there are any quality problems or failures, the
qualifying activity may require resumption of the original test frequency. Group C thermal shock is not required
if thermal shock (mounted) was done as part of group A inspection.
2/ If the manufacturer can demonstrate that this test has been performed five consecutive times with zero failures,
this test, with the approval of the qualifying activity, can be deleted. The manufacturer, however, shall perform
this test every 3 years after the deletion as part of long term design verification. If the design, material,
construction or processing of the part is changed or, if there are any quality problems, the qualifying activity may
require resumption of the specified testing. Deletion of testing does not relieve the manufacturer from meeting
the test requirements in case of dispute.
4.7 Methods of inspection and test.
4.7.1 Mounting for testing. Mounting is optional for test environments; however, when specified in the test
procedures, the chip capacitors shall be mounted on a suitable substrate (e.g., 96 percent alumina, G30 or FR4 glass
epoxy). The substrate material shall be such that it shall not be the cause of, nor contribute to, failure of any test for
which it may be used. The capacitors shall be mounted on the substrate as follows:
a. A substrate shall be prepared with metallized surface land areas of proper spacing to permit mounting of
chips by soldering the terminations of the chips to the "test card" land areas.
b. Solder paste shall be applied to terminals and substrates as applicable or alternative reflow techniques may
be used.
c. The chip shall then be placed across the metallized land areas of the test substrate so as to make contact
between chip and substrate land areas.
d. The substrate shall be exposed to +135°C ±15°C for a minimum of 1 minute. The substrate shall then be
transitioned to +245°C ±5°C. The substrate shall remain at +245°C ±5°C until the solder paste melts and
reflows forming a homogenous solder bond to the metallized substrate.
e. All excess flux or solder shall be removed.
22
For Parts Inquires submit RFQ to Parts Hangar, Inc.
© Copyright 2015 Integrated Publishing, Inc.
A Service Disabled Veteran Owned Small Business